What is AS9100?
Understanding standards like AS9100 can seem like a minefield. With all the different terms around it, from AS9100D and AS9100 Rev D to ISO 9001- you may be wondering exactly what is AS9100, what the differences are between all these terms, and what is required of you to comply.
Put simply, AS9100 is an international standard that outlines quality management system (QMS) requirements for the aerospace industry. It’s essentially an industry specific version of ISO 9001, adopted to include specific considerations for aerospace and defence organizations.
Let’s explore this further.
AS9100: key things to know
The AS9100 standard sets out the requirements for quality management systems that help aerospace organizations to design, create and provide safe and reliable products that meet customer, legal and regulatory expectations.
Created by the International Aerospace Quality Group (IAQG) and the Society of Automotive Engineers International (SAE), AS9100 is recognized across the globe and by industry giants such as the Federal Aviation Administration, US Department of Defence, and NASA. Since it was first introduced in 1997, the standard has gone through numerous revisions. The latest revision is AS9100 Rev D, or simply AS9100D, which was introduced in 2016.
AS9100 Rev D, like the versions that came before it, is based on ISO 9001. If you are not already aware, ISO 9001 is a standard from the International Organisation for Standardization. It provides generic QMS requirements for any organization irrespective of their industry or size. AS9100 is the same as ISO 9001, except that it has additional aerospace-specific requirements that make the QMS requirements more relevant for the aerospace industry.
What are the similarities between ISO 9001 and AS9100?
Both AS9100 and ISO 9001 are intended for organizations who need to show that they can provide products and services in compliance with customer, statutory and regulatory requirements. They are also relevant for organizations who want to improve their performance and customer satisfaction. Like ISO 9001, AS9100 can be used by organizations of any size.
AS9100 follows ISO 9001’s structure, dividing the standard into 10 clauses. The main clauses to be aware of are summarized below:
Context of the organization
Consider all issues that can impact your strategic objectives and how you plan your QMS. Concentrate on factors and conditions that affect your products, services, investments and interested parties, and make sure your QMS is appropriate for your organization.
Leadership
This requires the organization as a whole to demonstrate leadership from the top down when it comes to quality management, rather than it being one team or individual’s responsibility. Take accountability for the effectiveness of your QMS and promote a culture of quality throughout your organization.
Planning
Address any risks and opportunities, define your QMS objectives and how you will achieve them, and plan for and manage any changes. This is key to getting the most out of your QMS to ensure it works in the way you want, rather than acting as a necessary box to be ticked off in your compliance activity list.
Support
Consider what resources you need to support your QMS and provide these. Ensure employees are competent in their roles and have a sound awareness of the QMS and how it relates to them. Plan and executive effective communications, and ensure that you document information required by AS9100.
Operations
Plan and implement controls for all of your operational processes. Establish products and services requirements, carry out a proper design and development process, and control externally provided processes, products and services. Other requirements include performing production and service provision in a controlled environment, and not distributing products and services until they have been verified. You should also take action to spot and manage non-conformances.
Performance evaluation
Evaluate the performance of your QMS by considering what you will measure, who will measure it, how this will be done and when. You should establish a way to measure customer satisfaction, which AS9100 seeks to improve, and management must review the QMS at regular stages.
Improvement
Identify improvement opportunities, document your process for handling non-conformities, and work to constantly improve your QMS. This stage is valuable for gathering insights into how you can improve things organization-wide, and easily roll out those process changes using the tools available in your QMS.
What is the difference between ISO 9001 and AS9100?
In addition to the above, there are specific AS9100 requirements to fulfil the industry’s particular needs. These include measures that effect the following five areas:
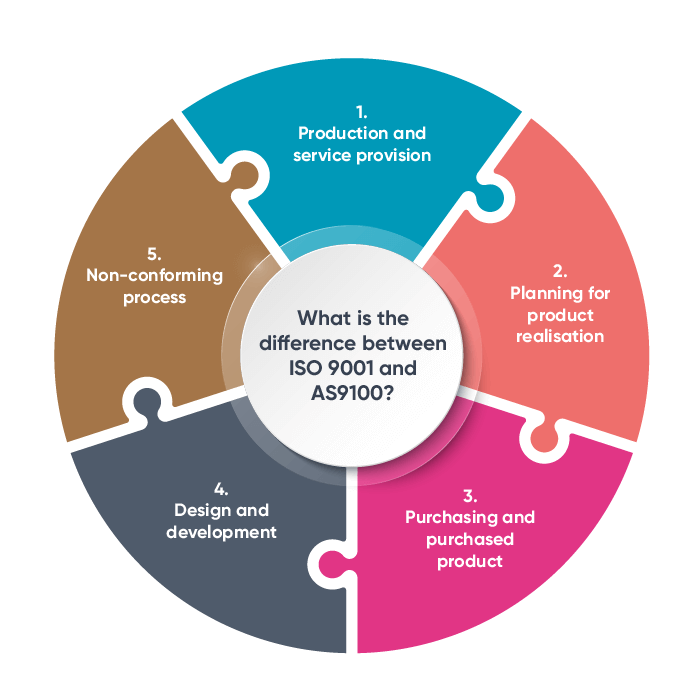
1. Production and service provision
Verify production processes and equipment and control any changes to these, and provide post-delivery support. There are also additional requirements on measures for product preservation and shelf-life control.
2. Planning for product realisation
These requirements relate to project management, the risk management process, configuration management of products, and control of work transfers to and between facilities and suppliers.
3. Purchasing and purchased product
Further controls on suppliers are required, such as inspections, audits, and First Article Inspection Reports. Extra purchasing information for suppliers is also required, and there is an additional control on purchased product that is released in a limited or controlled way prior to the completion of verification activities.
4. Design and development
These requirements impact the testing and documentation of the design verification and validation stages.
5. Non-conforming process
AS9100 provides further requirements when dealing with non-conformances. If you find a non-conformance in your products or processes, you must take action to correct them.
How can you become certified with AS9100?
You will need to adopt a quality management system that fulfils the AS9100 requirements. A registrar will then carry out an audit to confirm that you have fulfilled the obligations outlined in the standard. If you pass, you will become AS9100 certified. It is important that you consistently maintain and improve your quality management system, even after becoming certified. This will not only help you stay compliant, but it will ensure that your organization continues to excel.
Now that you understand the basics of ‘What is AS9100?’, find out how our AS9100 solution can support you.
Nicola spends her days thinking about how teams work better together —and how we can make document collaboration a little less painful with technology. She's particularly interested in helping teams within highly regulated industries, where data security and compliance are paramount, to streamline their processes and boost efficiency.